text.skipToContent
text.skipToNavigation
The availability of machines and plants is a basic requirement for productivity. In order to minimize unplanned downtimes, it is necessary to detect the sources of error at an early stage. This is exactly where SIPLUS CMS Condition Monitoring Systems come in: they continuously monitor the condition of mechanical components of your machines – even throughout the entire plant. SIPLUS CMS therefore represents an important step toward the digital factory, where all the players including machines, products and people along the value chain will be networked. SIPLUS CMS working together with MindSphere – the cloud-based, open IoT operating system from Siemens – opens up completely new possibilities. The powerful cloud platform is designed for analyzing large quantities of data and enables machine parks all over the world to be monitored for service purposes in order to reduce their downtimes.
SIPLUS CMS Condition Monitoring Systems create the prerequisites for the early detection of damage to machines and plants and the targeted planning of maintenance work – for a minimum of downtimes.
SIPLUS CMS records and analyzes mechanical variables from machines, integrates them into the automation world, and provides decision-making aids to maintenance staff, operators, and management. The open system architecture and the efficient interaction between all automation components (TIA) enable plant-wide condition monitoring of mechanical components across all levels. With this approach, control centers are able to closely monitor up-to-date status information. In the event of an anomaly, it is possible to quickly estimate how much longer secure operation is possible. Also anomalies in a plant can be compared directly to the condition of surrounding components to determine whether an increase in temperature is an indication of a bearing overheating.
SIPLUS CMS – Stepping up your production
Get digital added value from mechanical condition data
The availability of machines and plants is a basic requirement for productivity. In order to minimize unplanned downtimes, it is necessary to detect the sources of error at an early stage. This is exactly where SIPLUS CMS Condition Monitoring Systems come in: they continuously monitor the condition of mechanical components of your machines – even throughout the entire plant. SIPLUS CMS therefore represents an important step toward the digital factory, where all the players including machines, products and people along the value chain will be networked. SIPLUS CMS working together with MindSphere – the cloud-based, open IoT operating system from Siemens – opens up completely new possibilities. The powerful cloud platform is designed for analyzing large quantities of data and enables machine parks all over the world to be monitored for service purposes in order to reduce their downtimes.
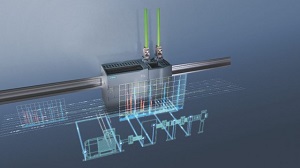
Acting with foresight – increasing availability
SIPLUS CMS Condition Monitoring Systems create the prerequisites for the early detection of damage to machines and plants and the targeted planning of maintenance work – for a minimum of downtimes.
Transparency across all levels – with Totally Integrated Automation (TIA)
SIPLUS CMS records and analyzes mechanical variables from machines, integrates them into the automation world, and provides decision-making aids to maintenance staff, operators, and management. The open system architecture and the efficient interaction between all automation components (TIA) enable plant-wide condition monitoring of mechanical components across all levels. With this approach, control centers are able to closely monitor up-to-date status information. In the event of an anomaly, it is possible to quickly estimate how much longer secure operation is possible. Also anomalies in a plant can be compared directly to the condition of surrounding components to determine whether an increase in temperature is an indication of a bearing overheating.
Your benefits
SIPLUS CMS is available in three different versions – from compact and integrated to modular and powerful. Regardless of which version you choose, you benefit from many advantages.
System benefits
- Simple system configuration
- Open standards
- Easy expandability
Cost reduction
- Longer lifecycle time
- Effective spare parts maintenance
- Investment protection
Higher productivity
- Higher availability
- Predictable maintenance and repair
- Simple diagnostics
Part of digitalization
- Record and analyze mechanical variables
- Connection to cloud solutions
- Decision-making aids for service
Seven steps to a customized Condition Monitoring (CM) solution
- Choosing the right Condition Monitoring System takes some planning. Use the following step-by-step guide to find the right Condition Monitoring solution for your needs:
- Define requirements: Decide which mechanical components must be monitored for what kinds of damage.
- Select a CM system: Choose the device with the right number of sensors and the right characteristics.
- Connect sensors and CM system: Note the maximum cable length when fixing the sensors.
- Choose method of analysis: Choose the right method from parameter-based, frequency-selective, or freely configurable analysis.
- Put the CM system into operation: Establish alarm and warning thresholds as per ISO 10816-3.
- Put control system with CM into operation: Decide which CM data must be visualized, and for whom.
- Optimize warning and alarm limits: Adjust warning and alarm limits based on initial trend curves with the system in operation.
- Benefit from all the advantages of MindSphere with MindConnect Edge Analytics based on CMS X-Tools.
You might also be interested in this:
SIMATIC Field PG M5
Read further
SIMATIC Field PG Latest generation of high-performance programming devices in a semi ruggedized notebook design The SIMATIC Field PG with its robust magnesium housing is well prepared for mobile applications in harsh environments: Shocks and vibrations, but also electromagnetic disturbances in machine-oriented industrial environments do not affect the device. Equipped with all important automation interfaces, the connection to machines and systems is possible via PROFIBUS as well as via two fast PROFINET interfaces. Serial connections are also supported. The SIMATIC memory cards can be deleted and programmed directly in the corresponding slots. The pre-installed engineering software makes the SIMATIC Field PG ready for immediate use. The TIA Portal simplifies fast and efficient configuring, commissioning, service and maintenance. The SIMATIC Field PG is available in two performance choices: Comfort and Advanced
Siemens Sitop
Read further
When it comes to electricity, you can stay with the old. Or benefit from the new standard. Experience the start of a new chapter in the world of standard power supplies with the SITOP PSU6200 all-around power supply. Whether you’re a builder or operator of control panels, machines, or plants, all users benefit from the ingenious functions and features of the new SITOP PSU6200 product line – throughout the entire lifecycle, from planning and engineering to installation and operation.
Schneider Electric XIOT
Read further
The Internet of Things is the extension of the Internet to connected devices. Telemecanique Sensors offers a wireless solution to collect data from remote equipment and use this data, via the Internet, on a PC or mobile device. The XIOT Cloud connected switch from Telemecanique Sensors is based on LPWAN \(low power wide area network\) technology, operated by Sigfox. The Sigfox network covers 32 countries and is already very extensive in Europe. It is also being rapidly deployed in the US and Asia-Pacific. It uses antennas with a range of around 50 km. The map on the Sigfox website shows exactly which areas are covered by the Network.
Phoenix Contact Axioline
Read further
The modular station communicates with a PROFINET controller, e.g., a distributed control system, via a bus coupler. As an option, up to eight PROFIBUS PA segments can be connected to the individual proxy outlets in a compact way. To ensure the individual segments are immune to interference, appropriate shield connection technology is available.
Check out our other success stories:
-
TR Service - Future-proof low-voltage panelRead moreTR-Service provides industrial maintenance using all disciplines, from electrical and mechanical to hydraulic and pneumatic. With support from Breemes, the company installed a large low-voltage panel. ‘After discussing my summary plan with them, I decided to just do it,’ says director-owner Raoul Tielens. At Breemes' suggestion, the panel was future-proofed by preparing it for power monitoring.
-
Peeters - Young Company, New EquipmentRead moreSince its founding a few years ago, Peeters Robotic Solutions has been rapidly developing, working on projects both domestically and internationally and providing standard solutions for industrial palletizing. The company stays up to date with the latest technology, including Festo’s electrical and pneumatic drives. To achieve this, it relies on itsme. “Thanks to their expertise and skills, we can bring innovation to the forefront for our customers.”
-
Kusters - Putting weight behind itRead moreKusters was looking for a weighing solution for its banknote devaluation machines that was easy to integrate into the Siemens control system. Through itsme, they came into contact with the right knowledge carriers at Siemens. ‘For us as Kusters, itsme is not only a supplier but also a source of knowledge, with which we co-engineer certain components and process steps, such as this weighing system.’
-
Eneco - Green light for green electricity and steamRead moreEneco Bio Golden Raand, located in the port area of Delfzijl, converts biomass into green electricity and green steam. Each year, the plant processes approximately 300,000 tons of waste wood from the Netherlands and neighboring countries. As part of Eneco’s climate ambitions, a project began in 2022 to replace the existing fluorescent lighting in and around the boiler room. The project was carried out under the supervision of itsme. “Two factors were important in this process: the cost, of course, but also the level of service.”
Why not take a look at these trainings we offer:
-
PROFINET CPNERead moreavailable in Dutch
-
PROFIBUS CPERead moreavailable in Dutch
-
WinCC-SCADA2Read moreavailable in Dutch
-
PCS7-SAFE V9Read moreavailable in Dutch