text.skipToContent
text.skipToNavigation
Food grade is commonly considered to be the equivalent of having food-grade seals, food-grade lubricant and corrosion-resistant bearing units.
SKF's current generation of bearing units are already food-grade products and are relubrication-free.
However, we are now raising the bar to support pro-active food safety by providing food-safe bearing units that are completely sealed (Blue range), lubricated for life and designed for increased bearing performance, even in the harshest processing and cleaning environments.
Hygienic design and complete seal ability for better cleanliness. The blue colour makes it easier to detect potential contaminants.
Work proactively to reduce food safety risks by combining hygienic design, relubrication-free technology, corrosion resistant and food grade components. The bearing units are sealed both from the front and from behind. All units have an allergen-free grease fill.
For example, re-lubricating 100 bearing positions on a weekly basis requires 70 kg of lubricant/year. Not mentioning the labor to apply it.
33% less water use, energy saved, waste avoidance
You can achieve environmental gains, for example 33% less water used for cleaning hygienically designed open bearings compared to standard relubricable units and no disposal of grease absorbants.
SKF Food Line ball bearing units
From food grade to food safe
Food grade is commonly considered to be the equivalent of having food-grade seals, food-grade lubricant and corrosion-resistant bearing units. SKF's current generation of bearing units are already food-grade products and are relubrication-free.
However, we are now raising the bar to support pro-active food safety by providing food-safe bearing units that are completely sealed (Blue range), lubricated for life and designed for increased bearing performance, even in the harshest processing and cleaning environments.
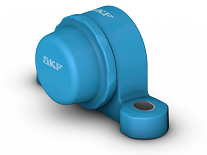
Reduce food safety risks with the new fully sealed Blue Range units
Hygienic design and complete seal ability for better cleanliness. The blue colour makes it easier to detect potential contaminants.
Work proactively to reduce food safety risks by combining hygienic design, relubrication-free technology, corrosion resistant and food grade components. The bearing units are sealed both from the front and from behind. All units have an allergen-free grease fill.
Reduce cost of maintenance and related costs
As the new ball bearing units have been designed for relubrication-free operation and increased performance even in harsh environments, you are able to reduce maintenance costs.For example, re-lubricating 100 bearing positions on a weekly basis requires 70 kg of lubricant/year. Not mentioning the labor to apply it.
33% less water use, energy saved, waste avoidance
You can achieve environmental gains, for example 33% less water used for cleaning hygienically designed open bearings compared to standard relubricable units and no disposal of grease absorbants.
You might also be interested in this:
Schneider Lexium 32 & Motors
Read further
The Lexium 32 range of servo drives includes four servo drive models with power ratings from 0.15 to 11 kW and the servo motor ranges BMH and BSH series
Siemens SIPLUS
Read further
The availability of machines and plants is a basic requirement for productivity. In order to minimize unplanned downtimes, it is necessary to detect the sources of error at an early stage. This is exactly where SIPLUS CMS Condition Monitoring Systems come in: they continuously monitor the condition of mechanical components of your machines – even throughout the entire plant. SIPLUS CMS therefore represents an important step toward the digital factory, where all the players including machines, products and people along the value chain will be networked. SIPLUS CMS working together with MindSphere – the cloud-based, open IoT operating system from Siemens – opens up completely new possibilities. The powerful cloud platform is designed for analyzing large quantities of data and enables machine parks all over the world to be monitored for service purposes in order to reduce their downtimes.
Schneider Electric XIOT
Read further
The Internet of Things is the extension of the Internet to connected devices. Telemecanique Sensors offers a wireless solution to collect data from remote equipment and use this data, via the Internet, on a PC or mobile device. The XIOT Cloud connected switch from Telemecanique Sensors is based on LPWAN \(low power wide area network\) technology, operated by Sigfox. The Sigfox network covers 32 countries and is already very extensive in Europe. It is also being rapidly deployed in the US and Asia-Pacific. It uses antennas with a range of around 50 km. The map on the Sigfox website shows exactly which areas are covered by the Network.
Pilz PSENOpt II
Read further
The second generation of light curtains, PSENopt II, provide safe access to the production process and provide finger, hand and body protection, depending on the requirement. The first Type 3 safety light curtains are specifically designed for applications up to PL d of EN/IEC 61496-1. Type 4 light curtains are also available for applications up to PL e in accordance with EN/IEC 61496-1/-2. As the units are so robust, PSENopt II sensors provide protection against shock, collision and vibration and so are suitable for use in rugged industrial environments. The operator can evaluate the essential causes and system defects responsible for the machine stop by means of the LEDs. Downtimes are reduced as a result.
Check out our other success stories:
-
TR Service - Future-proof low-voltage panelRead moreTR-Service provides industrial maintenance using all disciplines, from electrical and mechanical to hydraulic and pneumatic. With support from Breemes, the company installed a large low-voltage panel. ‘After discussing my summary plan with them, I decided to just do it,’ says director-owner Raoul Tielens. At Breemes' suggestion, the panel was future-proofed by preparing it for power monitoring.
-
Peeters - Young Company, New EquipmentRead moreSince its founding a few years ago, Peeters Robotic Solutions has been rapidly developing, working on projects both domestically and internationally and providing standard solutions for industrial palletizing. The company stays up to date with the latest technology, including Festo’s electrical and pneumatic drives. To achieve this, it relies on itsme. “Thanks to their expertise and skills, we can bring innovation to the forefront for our customers.”
-
Kusters - Putting weight behind itRead moreKusters was looking for a weighing solution for its banknote devaluation machines that was easy to integrate into the Siemens control system. Through itsme, they came into contact with the right knowledge carriers at Siemens. ‘For us as Kusters, itsme is not only a supplier but also a source of knowledge, with which we co-engineer certain components and process steps, such as this weighing system.’
-
Eneco - Green light for green electricity and steamRead moreEneco Bio Golden Raand, located in the port area of Delfzijl, converts biomass into green electricity and green steam. Each year, the plant processes approximately 300,000 tons of waste wood from the Netherlands and neighboring countries. As part of Eneco’s climate ambitions, a project began in 2022 to replace the existing fluorescent lighting in and around the boiler room. The project was carried out under the supervision of itsme. “Two factors were important in this process: the cost, of course, but also the level of service.”